Plastic extrusion for pipes, sections, and custom shapes
Recognizing the Fundamentals and Applications of Plastic Extrusion in Modern Manufacturing
In the world of contemporary manufacturing, the strategy of plastic extrusion plays a crucial duty. Deciphering the principles of this process discloses the real flexibility and possibility of plastic extrusion.
The Fundamentals of Plastic Extrusion Process
While it may show up complex, the basics of the plastic extrusion process are based on fairly uncomplicated concepts. It is a manufacturing process in which plastic is melted and after that shaped into a continual profile with a die. The raw plastic product, often in the kind of pellets, is fed into an extruder. Inside the extruder, the plastic goes through heat and stress, creating it to thaw. The molten plastic is then compelled through a designed opening, referred to as a die, to form a long, constant product. The extruded item is cooled and afterwards reduced to the desired length. The plastic extrusion process is extensively made use of in different markets as a result of its effectiveness, adaptability, and cost-effectiveness.
Various Kinds Of Plastic Extrusion Techniques
Structure upon the fundamental understanding of the plastic extrusion process, it is essential to explore the different strategies entailed in this manufacturing technique. The 2 key techniques are profile extrusion and sheet extrusion. In account extrusion, plastic is melted and developed right into a continual profile, frequently used to produce pipelines, poles, rails, and home window frameworks. In comparison, sheet extrusion creates huge, level sheets of plastic, which are generally further refined into items such as food packaging, shower drapes, and cars and truck parts. Each technique requires specialized equipment and specific control over temperature level and stress to ensure the plastic keeps its shape during cooling. Recognizing these methods is essential to using plastic extrusion efficiently in modern-day manufacturing.

The Function of Plastic Extrusion in the Automotive Market
An overwhelming bulk of parts in modern-day automobiles are items of the plastic extrusion process. This procedure has actually changed the automobile industry, changing it into a more efficient, cost-effective, and flexible manufacturing industry. Plastic extrusion is mostly utilized in the production of different auto parts such as bumpers, grills, door panels, and dashboard trim. The process provides an attire, consistent result, allowing makers to produce high-volume get rid of excellent precision and very little waste. The lightness of the extruded plastic components adds to the total reduction in automobile weight, enhancing fuel performance. The longevity and resistance of these parts to warm, cold, and influence enhance the longevity of cars. Hence, plastic extrusion plays a pivotal role in vehicle production.
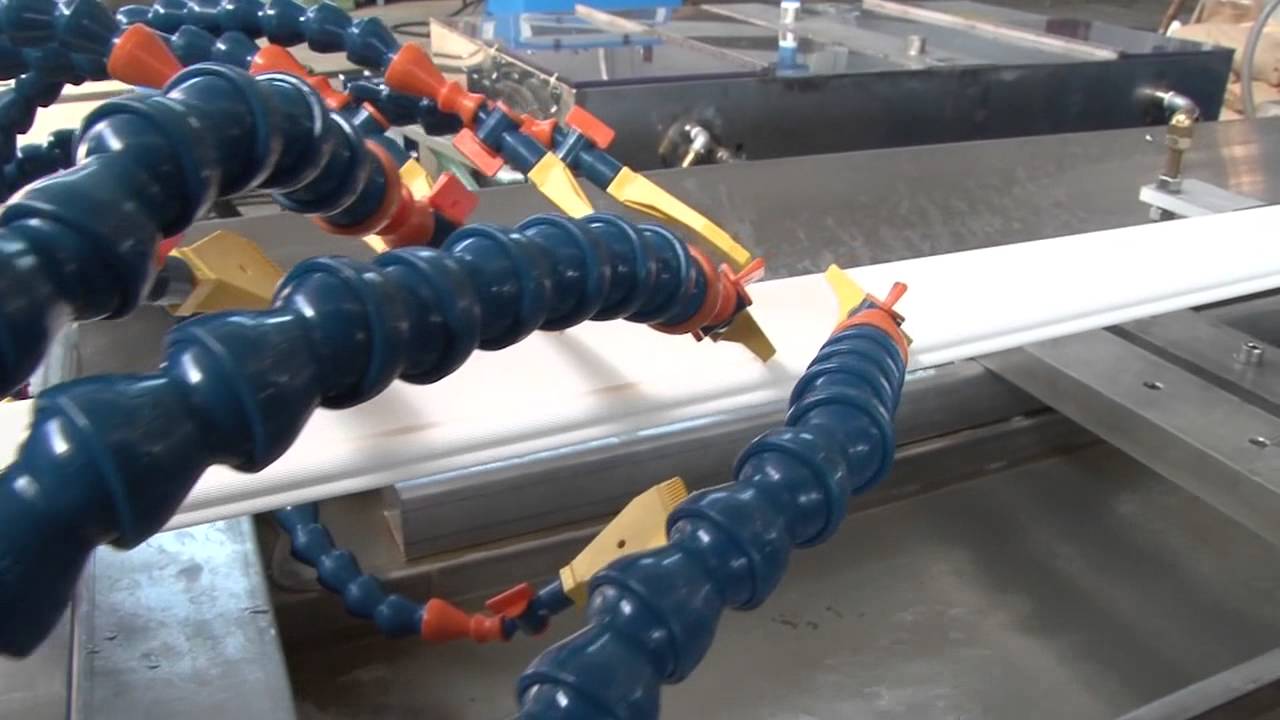
Applications of Plastic Extrusion in Durable Goods Manufacturing
Past its substantial influence on the automotive industry, plastic extrusion confirms special info similarly efficient in the realm of durable goods making. This process is vital in producing a broad array of items, from food product packaging to family appliances, toys, and also medical devices. The versatility of plastic extrusion permits makers to create and produce intricate forms and sizes with high accuracy and effectiveness. Furthermore, due to the recyclability of several plastics, extruded components can be recycled, minimizing here are the findings waste and cost. The flexibility, flexibility, and cost-effectiveness of plastic extrusion make it a preferred selection for numerous customer products suppliers, contributing considerably to the sector's growth and technology. Nevertheless, the environmental ramifications of this widespread usage require careful factor to consider, a topic to be gone over even more in the subsequent area.
Environmental Effect and Sustainability in Plastic Extrusion
The pervasive use of plastic extrusion in producing invites analysis of its eco-friendly ramifications. Efficient equipment decreases power use, while waste management systems reuse scrap plastic, reducing raw material needs. Despite these renovations, even more innovation is required to reduce the ecological footprint of plastic extrusion.
Verdict
In verdict, plastic extrusion plays a vital function in contemporary production, particularly in the auto and customer items fields. Understanding the basics of this process is key to optimizing its applications and benefits.

The plastic extrusion procedure is thoroughly utilized in various sectors due to its flexibility, cost-effectiveness, and performance.
Building upon the basic understanding of the plastic extrusion procedure, it is required to discover the different methods entailed in this manufacturing technique. plastic extrusion. In comparison, sheet extrusion develops big, flat sheets of plastic, Continued which are usually further processed right into products such as food product packaging, shower curtains, and cars and truck parts.A frustrating majority of components in modern lorries are products of the plastic extrusion procedure